Главный офис
в центре Европы
Гарантия
до 24 мес
до 24 мес
Лучшие
цены
цены
Экономия
от 15 до 55%
от 15 до 55%
Доставка
по России
по России
Все грузы
застрахованы
застрахованы
Бесплатная
доставка
доставка

Alfa Laval AlfaFlash
Категория - Выпарные системы
Официальный сайт Alfa Laval (Швеция) :
www.alfalaval.com
Узнать цену
В нашей компании вы можете выбрать и купить Alfa Laval AlfaFlash, а также другие запчасти от
компании Alfa Laval с доставкой по всей России, в том числе в ваш город : Дублин. Для запроса цен, сроков поставки
и других характеристик продукции Alfa Laval, пожалуйста, заполните форму обратной связи или пришлите описание необходимых Вам наименований
на электронный адрес info@famaga.ru
Описание
Продукция, изготовленная шведской Alfa Laval компанией, подходит для использования в пищевой, химической, фармацевтической, горнообрабатывающей и нефтяной промышленности.Преимуществом товара является длительный срок службы без необходимости осуществления регулярного обслуживания, а также его первоклассное качество и надежность. Alfa Laval AlfaFlash evaporation systems are designed for optimal fouling resistance. With numerous plants around the world, AlfaFlash is the well-proven reliable solution for concentrating stillage, corn steep liquor, salty effluents, fish and meat stick water and spent wash. The considerably higher shear rate (already at quite moderate flows) leads to substantially higher heat transfer efficiency, significantly lower pump costs and a more compact installation. Space saving AlfaFlash systems are compact with a low height and a low weight of the system. The compact size of AlfaFlash plate evaporators gives a lean installation and low installation costs. A range of AlfaFlash evaporators is available to suit different liquids and capacity requirements. High heat transfer efficiency Our reliable AlfaFlash evaporators offer a very high thermal efficiency. The considerably higher shear rate in the AlfaFlash evaporators – already at quite moderate flows – leads to a very high heat transfer efficiency, especially for shear thinning liquids. Viscous liquids AlfaFlash is beneficial in the evaporation of liquids having a high viscosity. The AlfaFlash evaporator is designed with a high wall shear to minimize viscosity, in the case of shear thinning liquids (the viscosity decreases with increased shear rate). In a multi-effect evaporation system the AlfaFlash is often used in the final concentration step as a finisher. Using AlfaFlash in one or more effects of an evaporation system makes it possible to reach very high final concentrations, even for liquids with a high viscosity. Maximized time intervals between cleaning AlfaFlash systems are designed to handle fouling liquids. The AlfaFlash plate evaporator in forced circulation mode gives high turbulence and high shear rate on the plate surfaces - giving a self-cleaning effect. This will cut down the fouling and increase the up time of the system. The heat transfer surfaces in the AlfaFlash plate evaporators are easily accessible for inspection or mechanical cleaning. Savings can be made since the AlfaFlash system requires less use of CIP cleaning chemicals and gives less waste water due to a low hold-up volume of the system. Benefits- Compact system
- Low fouling rate
- Long up-time
- Fast CIP cleaning
Пригласить на тендер
Наш менеджер свяжется с вами в ближайшее время.
Запрос отправлен
Запрос отправлен
Письмо не отправилось
Письмо не отправилось
Оставьте заявку
Мы свяжемся с вами и ответим на любой возникший вопрос.
Запрос отправлен
Запрос отправлен
Письмо не отправилось
Письмо не отправилось
Заказать звонок
Мы ответим на любые вопросы и поможем оформить заказ
Спасибо за вашу заявку!
А пока мы обрабатываем ваш запрос, вы можете найти другие необходимые вам позиции - ведь в нашем каталоге более 10 000 брендов!
Заказывая у нас сразу несколько позиций вы существенно экономите на доставке!
Каталог производителей
Искать
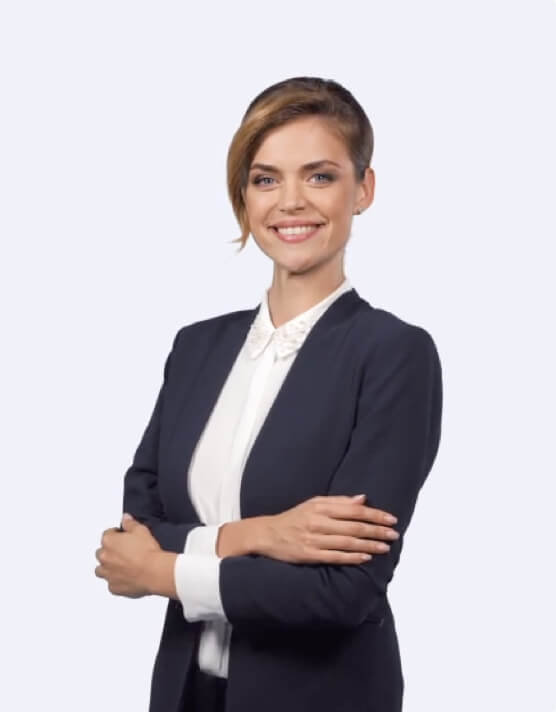
Что-то пошло не так
Кажется, что-то пошло не так. Попробуйте повторить попытку ещё раз позже.
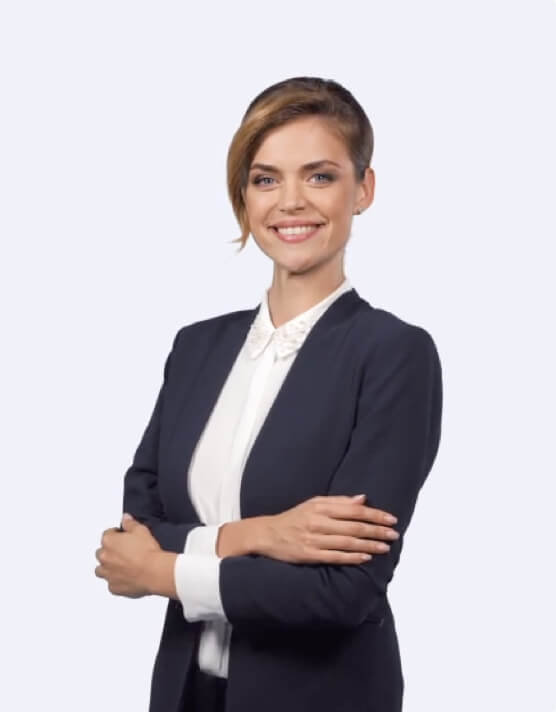